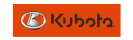

Optimize Your Productivity The KUHN OWR 6000 round bale inline wrapper offers exceptional wrapping productivity, while minimizing film and fuel use. This inline wrapper is designed for demanding farmers and custom operators looking for maximum productivity and profitability in a wrapper.
SPECIFICATIONS | OWR 6000 |
Round bale diameter | up to 72" (183 cm) |
Round bale width | 36" - 66" (91-168 cm) |
Square bale size | NA |
Max bale weight | 2,500 lbs (1,134 kg) |
Transport width | 9'5" (287 cm) |
Transport height | 9'11" (302 cm) |
Transport length | 20'1" (612 cm) |
Working length | 18'11" (576 cm) |
Machine net weight | 4,740 lbs (2,150 kg) |
Control | Electric controlled (VT 30) |
Film pre-stretcher | 2 x 30" (750 mm) (optional 4 × 30") |
Pre-stretch ratio | Approx. 70% standard (optional 60%) |
Road lights | Standard |
Front tires (drive) | 29 x 12.5-15 |
Rear tires | 11L x 15 8 Ply |
Braking system/compaction | Hydraulic braking |
Hydraulic capacity | 12 gal (45 L) |
Fuel tank capacity | 8 gal (30 L) |
Engine/Power | 13 hp Honda iGX standard (optional 20hp Honda iGX) |
Hoop speed | Variable |
Electric start | Standard |
Emergency stop | 2 locations |
Efficient Productivity
Patented, Conical Pre-Stretcher
Thirty-five years of KUHN wrapping heritage have proven these pre-stretchers in various conditions around the world. The standard pre-stretchers, which each hold a 30” (750 mm) roll, are made of aluminum to avoid build-up of tack from the film. Both outer ends of the aluminum rollers are cone-shaped to maintain the optimum width of the film and reduce the risk of film tear on the edges. The special ribbed profile of the aluminum rollers keeps air and water away from the film. The location of the pre-stretchers makes it very easy to change the film rolls. The standard pre-stretch of 70% is reached by a low-maintenance and low-noise gear transmission.
IntelliWrap™ Technology
Greater management and control of the wrapping process can be achieved by our unique IntelliWrap™ system. IntelliWrap uses simple electronics and efficient hydraulics to control the wrapping process and allows the operator to easily adjust film layers by one-layer increments. Settings such as film layers, seam layers, bale width and loading gap can digitally be set from the VT 30 monitor. Additionally, IntelliWrap records the bale count and the settings used for ten individual jobs, resulting in easy record keeping or billing for custom operators.
Efficient Power Use
The OWR 6000 features a standard 13-horsepower Honda iGX engine that automatically adjusts between high, medium and low idle depending on load, saving fuel. This wrapper also includes a priority hydraulic flow divider that controls the plunger and hoop drive together to rapidly feed bales into the wrapper, maximizing bales per hour. The priority hydraulic flow divider increases productivity and fuel savings by automatically adjusting the hoop and plunger speed depending on the number of film layers selected. Optimally allocating flow between the hoop and plunger, as film layers change, maximizes the hydraulic system performance and efficiency.
Propulsion & Steering
The OWR is equipped with a standard hydraulic propulsion and steering system. It can be driven using the levers in the control area or using the optional wireless remote.
Reliable, Easy Operation
BaleEye Sensor
The KUHN OWR 6000 inline wrapper features BaleEye, a sensor, that detects when a bale is present on the loading platform triggering the plunger and hoop cycle. Conveniently increase the loading delay via the monitor to give the operator more time to load the bale or decrease the delay to increase productivity. With this photoelectric solution the operator does not have to worry about this component wearing out, being affected by loose debris or not being able to detect odd-shaped bales as with competitive mechanical sensors.
Dual-Driven Hoop
The OWR 6000 features two propulsion wheels for optimal hoop traction in adverse conditions. Non-pneumatic drive wheels, made of industrial-grade polymer, are maintenance free and never go flat. Additionally, these drive wheels are designed with a concave surface, which partially surrounds the hoop, improving hoop stability and traction. The drive wheels also have a special grove creating a space for water to escape, ensuring the hoops stays spinning even in tough, wet conditions.
Transport
The OWR is easy to maneuver in transport configuration. The operator simply folds up the ramp tail and then extends the tongue. With the steering wheels centered and the machine hitched to the tractor, the operator simply raises the drive wheels, there are no drives to disengage. The OWR has a fixed hitch and rides only on the two rear tires making it easy to back up and position.
Safety
To ensure safe operation the OWR comes standard with two emergency buttons, one on each side of the machine. Additionally, the wireless remote has an emergency button. Whenever the door is opened to access the stretchers, the engine automatically shuts off, and the door also covers the control panel when open so the machine cannot be operated.
Preserve High-Quality Hay
Bale Compression
Compression of the bales in the tube is maintained utilizing the hydraulic system on the drive wheels. A simple dial and gauge allow the operator to adjust pressure in the system, pressing bales together to limit air spaces in the tube helping maintain feed value during storage.
Last Bale Push-Off
To maintain compression on the last bales of the tube a standard mechanical last bale push-off system is included.
From the normal operating position (left) the operator pivots the push plate 90 degrees (1), after cycling the plunger the first stage is extended (2). Then after cycling the plunger again the second stage is extended (3) and the plunger is cycled for the final time to push the last bale off the machine.
Request A Demo
Fields with asterisks* are required.